COALIA – Andro Vachon, Pascal Yves Vuillaume, Luc Deschamps, Lei Hu, Audrey Diouf Lewis, Pier-Luc Marcoux.
Partenaires financiers : CREPEC – CRSNG – FRQNT – Ministère de l’éducation et de l’enseignement supérieur, gouvernement du Québec – PRIMA Québec
Années de réalisation : 2022-2023
La technologie FFF : ses avantages et ses limitations
Le procédé de fabrication additive FFF (Fused Filament Fabrication) est aujourd’hui largement déployé dans le secteur industriel. Facile d’utilisation, cette technologie est disponible à coût abordable et ce, qu’il s’agisse des imprimantes ou de la matière première, généralement des thermoplastiques.
Toutefois, l’impression 3D FFF présente certaines limitations, soit :
● une mauvaise adhésion inter-couches,
● la présence de porosité dans la pièce imprimée,
● une faible précision dimensionnelle, un gauchissement et de possibles distorsions,
● un manque de qualité au niveau du fini de surface.
Ces contraintes sont en partie générées par les spécificités du procédé. En effet, outre le fait que les imprimantes FFF ne disposent pas de chambre d’impression conditionnée, des variations thermiques importantes sont observées lors du processus de déposition des polymères. Par conséquent, la technologie FFF augmente l’anisotropie de la pièce et compromet l’obtention des requis mécaniques ; une problématique de taille lorsqu’il s’agit d’imprimer des pièces fonctionnelles.
Contrôler le transfert thermique pour imprimer des pièces fonctionnelles
Afin d’obtenir des pièces de qualité alliant propriétés mécaniques et esthétiques, l’équipe de COALIA et ses partenaires ont émis l’hypothèse qu’une optimisation du transfert thermique de manière ponctuelle et localisée favoriserait l’adhésion inter-couches ou encore la surface de contact entre les filaments. Cela permettrait de réduire les taux d’anisotropie et la porosité.
Ainsi, chercheurs et industriels ont uni leur force et leur expertise pour développer un procédé de Fabrication par Dépôt de Filament Fondu avec Rayonnement (FFF-R). Ce dernier se compose d’un système de chauffage radiant annulaire monté sur le bloc chauffant d’une imprimante FFF standard. Cela permet de chauffer aussi bien le polymère avant son extrusion que la couche de déposition pour assurer l’adhésion entre les différentes couches de matériel.
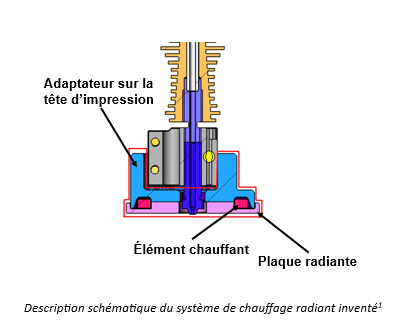
Une technologie facile d’utilisation et ouvrant la porte à un vaste choix de matériaux
Ce système peut être monté sur n’importe quelle imprimante FFF ; cette technologie se prête aussi bien aux polymères amorphes (PEI, PC, ABS, PAN, ASA, PMMA, PSU, PPSU, etc.) qu’aux élastomères thermoplastiques (TPE, TPU, TPC, TPA, TPS, composites, etc.) Nous avons à l’heure actuelle plusieurs projets en cours pour valider les bénéfices de cette technologie pour les polymères semi-cristallins (PLA, PA, PE, PP, PPS, PEEK, etc.).
Des résultats parlants
Impression d’éprouvettes en PEI (Ultem 1010)
Dans le cadre de ce développement, l’équipe de COALIA a imprimé des éprouvettes en PEI (Ultem 1010). Les tests mécaniques ont alors révélé :
● Rigidité (module de Young) : augmentation de 21 % pour une température du système radiant fixé à 390 oC et une vitesse d’impression de 35 mm / sec. (comparatif : impression sans chauffage radiant).
● Résistance à la traction : augmentation de 186 % selon l’axe de dépôt (Z) pour une température du système radiant fixé à 390 oC et une vitesse d’impression de 35 mm / sec. (comparatif : impression sans chauffage radiant).
● Ductilité : augmentation de 190 % selon l’axe de dépôt (Z) pour une température du système radiant de 390 oC et une vitesse d’impression de 35 mm / sec. (comparatif : impression sans chauffage radiant).
● Porosité : le procédé FFF-R permet de réduire le taux de porosité à 4 % à 390 oC vs un taux de porosité de 10% sans chauffage radiant.
● Qualité de la surface d’impression : redistribution des aspérités de surface, fusion des crêtes, réduction de la rugosité de surface de la pièce imprimée, diminution des défauts internes et des amorces de fissures.
Impression d’éprouvettes en ABS (ABS-M30)
Lors de l’impression 3D d’éprouvettes en ABS, il a été démontré que l’intégration du système radiant (comparatif : impression sans chauffage radiant) permet d’augmenter :
● La résistance en traction de 61 %.
● La rigidité de 5,5 %.
● L’élongation à la rupture de 110 %.
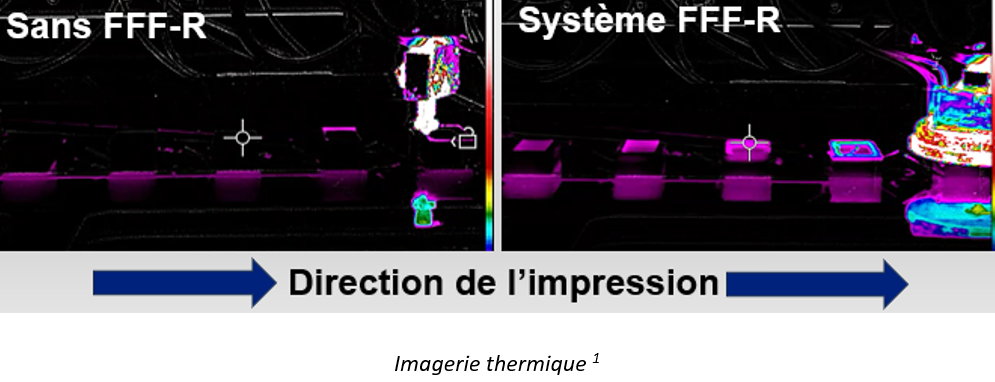
Une occasion pour les industriels de se démarquer
Le procédé FFF-R, tel que développé par COALIA, permet de réduire le taux de porosité des pièces imprimées, d’améliorer l’isotropie, de limiter le gauchissement notamment lors de la fabrication de pièces de grandes dimensions. Cette technologie permet déjà d’obtenir des pièces fonctionnelles répondant aux requis mécaniques (résistance à l’impact, à la flexion, déformation à la rupture, rigidité, taux de cristallinité, étanchéité).
En 2023, la technologie FFF‑R est brevetée par COALIA (CA 3177826; WO 2023/235959). Cette technologie représente une occasion pour les industriels d’accroître leur compétitivité, et ce à coût abordable. D’ailleurs, des entreprises de l’écosystème de la fabrication additive au Québec ont déjà montré leur intérêt, certain en se dotant d’une licence de commercialisation exclusive comme Fablab Inc. qui offrira sous peu des têtes d’impression dotées du module de COALIA, d’autres d’une licence d’utilisation.
1 Aucune reproduction n’est permise sans le consentement écrit de COALIA